Приспособление для сварки колец с трубами из титановых сплавов разработано и внедрено новаторами треста «Союзпромбуммонтаж». Сварка данных деталей требует надежной защиты не только лицевой, но и обратной стороны шва (корня).
Разработанное приспособление обеспечивает надежную двустороннюю газовую защиту сварного шва и автоматизирует процесс сварки. Стакан 8 приспособления (рис. 48) устанавливается на кольцо 12. Стакан можно поворачивать на 360° относительно трубы 13, с которой сваривается кольцо. Насадка 2 надевается на трубу 13 до плотного касания в нижнюю кромку кольца. В стакан под углом к оси впаяно сопло горелки 9 так, что выступающий электрод 6 попадает в зону стыка кольца 12 и трубы 13. В стакан вварена также трубка К), соединенная с кольцевой трубкой 5, расположенной над стыком. В коническую насадку 2 впаяна трубка 1.
Рис. 48. Приспособление для сварки.
Рис. 49. Электромагнитный клапан.
Перед сборкой деталей под сварку в трубу вставляется резиновая заглушка 15 с пальцем 16, служащим для ее извлечения. В процессе сварки защитный газ через трубку 10 поступает в кольцевую трубку 5 и через радиальные отверстия трубки 5 в зону сварки 4, заполняя при этом камеры 11 и 14 газ подается также через трубку 1 в камеру 3. Благодаря избыточному давлению в камерах 3, 11 14 создается надежная защита от окружающей атмосферы.
При сварке рабочий одной рукой держит горелку, а Другой равномерно поворачивает трубу. Через окно 7 в стакане осуществляется наблюдение за процессом Сварки. Для зажигания дуги без касания электрода с металлом в сварочную цепь включается осциллятор.
Внедрение этого приспособления обеспечило надежое получение качественного сварного соединения (хорошее формирование и высокая плотность шва) и повышение производительности труда. Применение для сварки флюса АНТ-17А дополнительно позволяет сокращать расход защитного газа.
Электромагнитный - клапан простой конструкции (рис. 49) разработан новаторами И. В. Писовым и Е. Ф. Лукиным. Клапан устраняет потери защитного газа при ведении аргоно-дуговой сварки в полевых и монтажных условиях. При отсутствии клапана такие потери газа неизбежны, так как подача его не прекращается при перерывах в процессе сварки в течение времени, необходимого для перекрытия вентиля на баллоне. Эти потери тем больше, чем дальше расположен пост от места сварки.
На втулку 5 клапана между дисками 1 и 11 намотан медный сварочный провод 4 сечением 25—30 мм2. В сварочную цепь обмотка включается последовательно контактами 2 и 12. На резьбовой конец втулки надет стакан 7 с вмонтированными штуцерами 9 и 10, а внутри втулки расположены стальной стержень 6 и пружина 3.
Рис. 50. Спаренный тройник для аргоно - дуговых установок
При отсутствии тока в обмотке отверстие в штуцере 9 закрыто пробковой вставкой 8, закрепленной на стержне 6. После зажигания дуги сварочный ток проходит через обмотку, а образованное магнитное поле втягивает стержень 6, сжимая пружину 3; отверстие в штуцере 9 открывается, и газ поступает к штуцеру 10 и далее к сварочной головке. Внедрение одного клапана позволяет экономить до 600 м3 газа в год.
Рис. 51. Расходомер газа.
Конструкция спаренного тройника (рис. 50) обеспечивает одновременное подключение к аргоно-дуговой установке двух горелок, которые могут быть включены в работу поочередно поворотом рукоятки тройника. Это сокращает затраты времени на переход при ведении сварочных работ (переналадку) с одной горелки на другую.
Тройник состоит из двух кранов (одного — для подачи охлаждающей воды и подвода сварочного тока, другого — для подачи защитного газа) и механизма их переключения.
Корпус 15 крана для подачи охлаждающей воды имеет штуцер 16 с наружной конической трубкой и центральным отверстием и два резьбовых отверстия 22 и 24, расположенных с двух сторон. Корпус 1 крана для подачи защитного газа имеет центральный штуцер 25 и два боковых штуцера 19 и 20.
Центральные отверстия корпусов 15 и 1 выполнены коническими, и в них установлены аналогичные конусные золотники, которые сверху поджаты накидными гайками 4 через втулки 5 и набивку 6.
Оба корпуса соединены между собой пластиной 2 при помощи гаек 3. На цилиндрических хвостовиках 7 золотников при помощи винтов 9 закреплены маховички 8, соединенные тягой 26 при помощи специальных винтов 17 и 18. Синхронный поворот золотников производится рукояткой 23 из изоляционного материала. Резьбой штуцера 16 тройник крепится на установке.
К отверстию 22 и штуцеру 20 присоединяются шланги одной горелки, а к отверстию 24 и штуцеру 19 — другой горелки. Через центральные отверстия штуцеров 25 и 16 подаются соответственно охлаждающая вода и газ. При нейтральном положении золотников (как показано на рис. 50) вода и газ не поступают к горелкам.
Рис. 52. Регулятор расхода газа.
При повороте рукоятки вправо на 45° до упора в штифт 21 каналы 10 и 11 сообщаются с камерами 14, а вода и газ поступают в горелку, подключенную с этой стороны. При переводе рукоятки на угол 45° от нейтрального положения влево совмещаются каналы 13 и 12, а вода и газ поступают в другую горелку. Корпус 1 является одновременно тоководом.
Внедрение спаренного тройника, кроме сокращения времени на переналадку, обеспечивает повышение срока службы присоединительных элементов.
Расходомер защитного газа (рис. 51) разработан новатором В. А. Воловичем. Он выполнен на базе манометра низкого давления от ацетиленового редуктора. Манометр 1 присоединен к корпусу 4 регулятора. В корпусе имеется входное отверстие 5, через которое газ подается в камеру давления и через штуцер 3 поступает в горелку. Регулировка расхода газа осуществляется резьбовой иглой 6 при вращении ее за рукоятку 7.
Камера давления собирается с улиткой манометра. Шкала 2 манометра оттарирована при помощи ротаметра на расход аргона и гелия.
Регулятор расхода газа несложен в изготовлении и надежей в работе. Он может быть подключен к любой установке в цеховых и монтажных условиях.
Регулятор расхода газа конструкции новаторов В. Б. Киселева и Ю. М. Васильева показан на рис. 52.
Рис. 53. Устройство для зачистки металла под сварку.
Узел регулировки размещен в корпусе 4, а для настройки расхода газа служат рукоятки 1, стрелка 2 и круговая шкала 3. Газ в регулятор поступает от сети через штуцер 6 и сменную тарированную шайбу 5. В комплекте с расходомером имеются две тарированные шайбы: одна обеспечивает пределы регулирования 7—20 л/мин, а вторая — 20—50 л/мин. На торце корпуса имеется выходное отверстие, через которое газ поступает в рабочую зону. Ограничитель 7 предотвращает возможность поворота рукоятки на угол более 360°.
Точность поддержания расхода газа составляет 5%.
Рассмотренные регуляторы повышают качество сваpных соединений и уменьшают непроизводительные потери газа.
Устройство для зачистки металла под сварку показано на рис. 53. Оно выполнено на базе шлифовальной машинки 2, которая при помощи хомута 1 закреплена на подвижной тележке. Тележка состоит из раздвижной рамы 8, снабженной двумя роликами: поддерживающим 7 и направляющим 5.
Устройство устанавливают роликами на обрабатываемый лист 6 и базируют буртиком направляющего ролика на кромке листа. После включения двигателя шлифовальный круг 4 прижимают к материалу поворотом машинки за рукоятку 9 и перемещают вдоль кромки листа. Для безопасности в работе шлифовальный круг закрыт кожухом 3.
Техническая характеристика
Максимальные размеры шлифовального круга, мм......... 150x25x32
Наибольшая частота вращения шпинделя, об/мин................5100
Давление воздуха на входе в машинку, кг/см2...................5
Усилие на рукоятке в процессе зачистки, кгс............Не более 6—7
Габаритные размеры....... 50x350x200
Масса, кг . . .....................5
Внедрение данного устройства обеспечило повышение производительности зачистки и улучшение качества обработанной поверхности. Устройство повышает культуру производства и безопасность обработки.
Автор - svarka
Разработанное приспособление обеспечивает надежную двустороннюю газовую защиту сварного шва и автоматизирует процесс сварки. Стакан 8 приспособления (рис. 48) устанавливается на кольцо 12. Стакан можно поворачивать на 360° относительно трубы 13, с которой сваривается кольцо. Насадка 2 надевается на трубу 13 до плотного касания в нижнюю кромку кольца. В стакан под углом к оси впаяно сопло горелки 9 так, что выступающий электрод 6 попадает в зону стыка кольца 12 и трубы 13. В стакан вварена также трубка К), соединенная с кольцевой трубкой 5, расположенной над стыком. В коническую насадку 2 впаяна трубка 1.
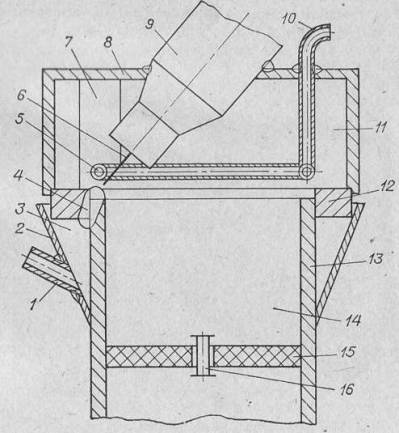
Рис. 48. Приспособление для сварки.
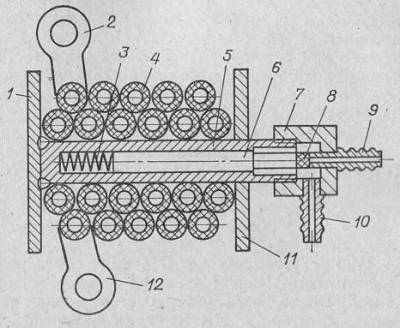
Рис. 49. Электромагнитный клапан.
Перед сборкой деталей под сварку в трубу вставляется резиновая заглушка 15 с пальцем 16, служащим для ее извлечения. В процессе сварки защитный газ через трубку 10 поступает в кольцевую трубку 5 и через радиальные отверстия трубки 5 в зону сварки 4, заполняя при этом камеры 11 и 14 газ подается также через трубку 1 в камеру 3. Благодаря избыточному давлению в камерах 3, 11 14 создается надежная защита от окружающей атмосферы.
При сварке рабочий одной рукой держит горелку, а Другой равномерно поворачивает трубу. Через окно 7 в стакане осуществляется наблюдение за процессом Сварки. Для зажигания дуги без касания электрода с металлом в сварочную цепь включается осциллятор.
Внедрение этого приспособления обеспечило надежое получение качественного сварного соединения (хорошее формирование и высокая плотность шва) и повышение производительности труда. Применение для сварки флюса АНТ-17А дополнительно позволяет сокращать расход защитного газа.
Электромагнитный - клапан простой конструкции (рис. 49) разработан новаторами И. В. Писовым и Е. Ф. Лукиным. Клапан устраняет потери защитного газа при ведении аргоно-дуговой сварки в полевых и монтажных условиях. При отсутствии клапана такие потери газа неизбежны, так как подача его не прекращается при перерывах в процессе сварки в течение времени, необходимого для перекрытия вентиля на баллоне. Эти потери тем больше, чем дальше расположен пост от места сварки.
На втулку 5 клапана между дисками 1 и 11 намотан медный сварочный провод 4 сечением 25—30 мм2. В сварочную цепь обмотка включается последовательно контактами 2 и 12. На резьбовой конец втулки надет стакан 7 с вмонтированными штуцерами 9 и 10, а внутри втулки расположены стальной стержень 6 и пружина 3.
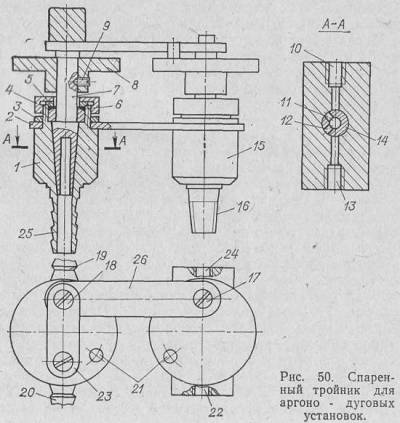
Рис. 50. Спаренный тройник для аргоно - дуговых установок
При отсутствии тока в обмотке отверстие в штуцере 9 закрыто пробковой вставкой 8, закрепленной на стержне 6. После зажигания дуги сварочный ток проходит через обмотку, а образованное магнитное поле втягивает стержень 6, сжимая пружину 3; отверстие в штуцере 9 открывается, и газ поступает к штуцеру 10 и далее к сварочной головке. Внедрение одного клапана позволяет экономить до 600 м3 газа в год.
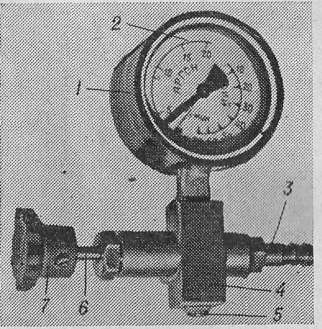
Рис. 51. Расходомер газа.
Конструкция спаренного тройника (рис. 50) обеспечивает одновременное подключение к аргоно-дуговой установке двух горелок, которые могут быть включены в работу поочередно поворотом рукоятки тройника. Это сокращает затраты времени на переход при ведении сварочных работ (переналадку) с одной горелки на другую.
Тройник состоит из двух кранов (одного — для подачи охлаждающей воды и подвода сварочного тока, другого — для подачи защитного газа) и механизма их переключения.
Корпус 15 крана для подачи охлаждающей воды имеет штуцер 16 с наружной конической трубкой и центральным отверстием и два резьбовых отверстия 22 и 24, расположенных с двух сторон. Корпус 1 крана для подачи защитного газа имеет центральный штуцер 25 и два боковых штуцера 19 и 20.
Центральные отверстия корпусов 15 и 1 выполнены коническими, и в них установлены аналогичные конусные золотники, которые сверху поджаты накидными гайками 4 через втулки 5 и набивку 6.
Оба корпуса соединены между собой пластиной 2 при помощи гаек 3. На цилиндрических хвостовиках 7 золотников при помощи винтов 9 закреплены маховички 8, соединенные тягой 26 при помощи специальных винтов 17 и 18. Синхронный поворот золотников производится рукояткой 23 из изоляционного материала. Резьбой штуцера 16 тройник крепится на установке.
К отверстию 22 и штуцеру 20 присоединяются шланги одной горелки, а к отверстию 24 и штуцеру 19 — другой горелки. Через центральные отверстия штуцеров 25 и 16 подаются соответственно охлаждающая вода и газ. При нейтральном положении золотников (как показано на рис. 50) вода и газ не поступают к горелкам.
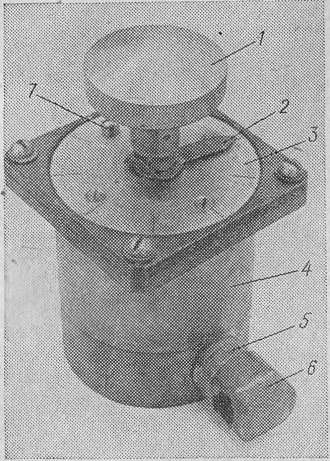
Рис. 52. Регулятор расхода газа.
При повороте рукоятки вправо на 45° до упора в штифт 21 каналы 10 и 11 сообщаются с камерами 14, а вода и газ поступают в горелку, подключенную с этой стороны. При переводе рукоятки на угол 45° от нейтрального положения влево совмещаются каналы 13 и 12, а вода и газ поступают в другую горелку. Корпус 1 является одновременно тоководом.
Внедрение спаренного тройника, кроме сокращения времени на переналадку, обеспечивает повышение срока службы присоединительных элементов.
Расходомер защитного газа (рис. 51) разработан новатором В. А. Воловичем. Он выполнен на базе манометра низкого давления от ацетиленового редуктора. Манометр 1 присоединен к корпусу 4 регулятора. В корпусе имеется входное отверстие 5, через которое газ подается в камеру давления и через штуцер 3 поступает в горелку. Регулировка расхода газа осуществляется резьбовой иглой 6 при вращении ее за рукоятку 7.
Камера давления собирается с улиткой манометра. Шкала 2 манометра оттарирована при помощи ротаметра на расход аргона и гелия.
Регулятор расхода газа несложен в изготовлении и надежей в работе. Он может быть подключен к любой установке в цеховых и монтажных условиях.
Регулятор расхода газа конструкции новаторов В. Б. Киселева и Ю. М. Васильева показан на рис. 52.
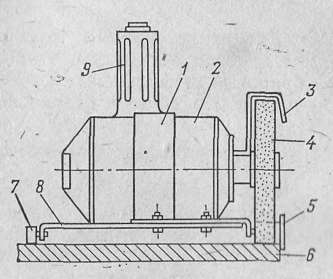
Рис. 53. Устройство для зачистки металла под сварку.
Узел регулировки размещен в корпусе 4, а для настройки расхода газа служат рукоятки 1, стрелка 2 и круговая шкала 3. Газ в регулятор поступает от сети через штуцер 6 и сменную тарированную шайбу 5. В комплекте с расходомером имеются две тарированные шайбы: одна обеспечивает пределы регулирования 7—20 л/мин, а вторая — 20—50 л/мин. На торце корпуса имеется выходное отверстие, через которое газ поступает в рабочую зону. Ограничитель 7 предотвращает возможность поворота рукоятки на угол более 360°.
Точность поддержания расхода газа составляет 5%.
Рассмотренные регуляторы повышают качество сваpных соединений и уменьшают непроизводительные потери газа.
Устройство для зачистки металла под сварку показано на рис. 53. Оно выполнено на базе шлифовальной машинки 2, которая при помощи хомута 1 закреплена на подвижной тележке. Тележка состоит из раздвижной рамы 8, снабженной двумя роликами: поддерживающим 7 и направляющим 5.
Устройство устанавливают роликами на обрабатываемый лист 6 и базируют буртиком направляющего ролика на кромке листа. После включения двигателя шлифовальный круг 4 прижимают к материалу поворотом машинки за рукоятку 9 и перемещают вдоль кромки листа. Для безопасности в работе шлифовальный круг закрыт кожухом 3.
Техническая характеристика
Максимальные размеры шлифовального круга, мм......... 150x25x32
Наибольшая частота вращения шпинделя, об/мин................5100
Давление воздуха на входе в машинку, кг/см2...................5
Усилие на рукоятке в процессе зачистки, кгс............Не более 6—7
Габаритные размеры....... 50x350x200
Масса, кг . . .....................5
Внедрение данного устройства обеспечило повышение производительности зачистки и улучшение качества обработанной поверхности. Устройство повышает культуру производства и безопасность обработки.
Автор - svarka
- Войдите, чтобы оставлять комментарии